Implementation of the Pimcore system for information management
Oct 16, 2024 • 5 min read
Company Overview
Olma, a company with a 77-year tradition, is renowned for its extensive range of industrial lubricants, vehicle lubricants and various additives like AdBlue (cooling lubricant additives, quench oil additives, etc.). The company’s core activities include the development, production, marketing and maintenance of all types of lubricants and consulting their users about the correct application.
Olma’s lubricant sales are targeted at the Southeast European market, where it ensures user support with high-quality products and expert services. In Slovenia, Olma holds over 43% of the industrial lubricant market share.
Challenge
As Olma expanded, the number of samples, products and brands grew, leading to an increase in the number of documents that needed to be maintained and updated. This was compounded by the use of multiple programs for different purposes. Updating documents became a laborious process requiring manual searches for the latest Word or Excel versions, making it highly time-consuming and inefficient.
These documents with essential product data were crucial for the effective functioning of various departments. Without a clear, centralized source of information, errors, delays and inconsistencies across channels and departments were frequent.
These documents served as sources for various product details, technical sheets, catalogs, etc., and inconsistencies often arose between technical sheets and sales catalogs.
Thus, Olma needed to implement a solution for a centralized product information management, enhancing data accuracy and efficiency.
Objective
The main objective of the project was to optimize workflows and remove bottlenecks in data enrichment processes. Prior to the implementation of the Pimcore system, product data was sourced from multiple channels, including:
- ERP system,
- chemical regulatory system,
- Excel documents,
- Word documents,
- documents from suppliers,
- various internal documents,
- marketing materials (images, videos, etc.).
Product data included:
- product names and descriptions,
- packaging methods,
- ADR data (dangerous goods transport data),
- chemical properties,
- physical product properties,
- storage methods,
- visual and video materials,
- measurement methods (laboratory services).
An example of the previous data management system for a specific product:
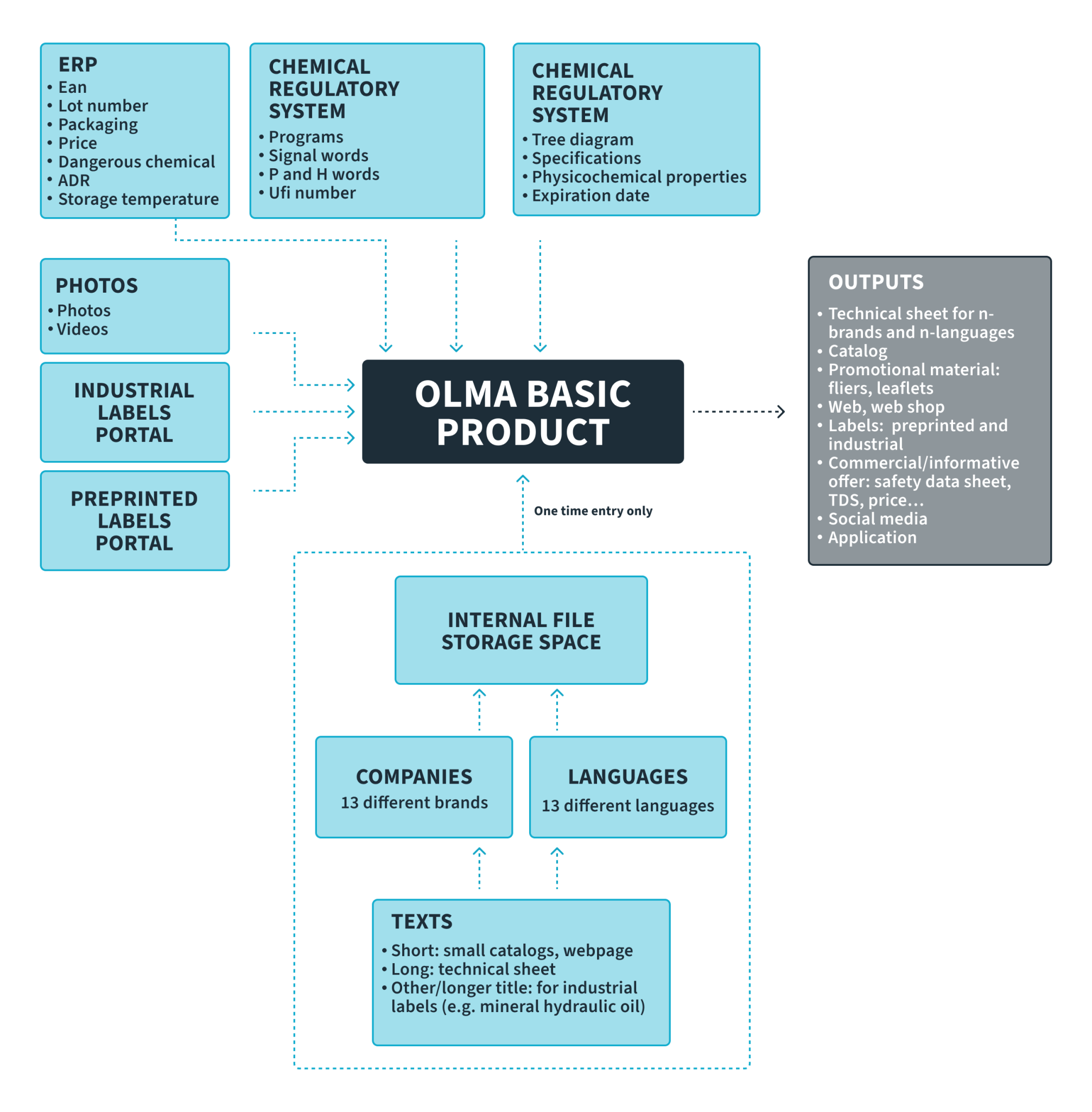
Starting to solve the challenges
Our every project begins with a discovery phase that involves an in-depth understanding of current data management processes, goals and challenges. For Olma, this phase included several workshops and resulted in a detailed project solution, along with technical and functional project plans. This phase lasted approximately two months, involving a team of a PIM solution architect, a technical project manager and a lead developer, alongside representatives from Olma’s data management departments.
The discovery phase is vital as it forms the foundation for customized solutions tailored to company needs.
Why the discovery phase is essential for successful project
The discovery phase is the essential first step in complex project development, like implementing a Product Information Management (PIM) system. It includes workshops that gather necessary information about the company, processes, goals, and challenges and results in an implementation proposal that highlights risks and lays a solid groundwork for the project.
Based on our project management experience, we structured discovery phase in these stages:
- New application/solution processes review:
- Analysis of current document preparation processes and product data management.
- Setting rules for publishing and managing content.
- Data model application:
- Overview of data structure, data document model and product information.
- Definition of attributes and rules for document content enrichment.
- Linking data objects and defining relationships and dependencies between them.
- Mapping data objects and defining process automation rules.
- Data capture and system integration:
- Identification and inventory of input data formats and data capture planning.
- Review of back-end systems and integrations planning, including connection services planning.
- Project plan development:
- Development of technical and functional specification, user scenarios, data model and data capture and integration plan.
- Determination of the implementation timeline and assessment of the financial costs of the project.
The results of the research phase are a rich source of information that enables the development of customized solutions, fully compatible with the company’s business needs. The phase includes a series of workshops and (not necessarily) also interviews, through which we get insights into the company’s operations, processes, business model, competition and other key factors. Based on these findings, we create a detailed project plan that includes an inventory of technical and user requirements, a timeline and a financial plan.
Technical and functional specifications
The technical and functional specification is a fundamental document that describes in detail how the PIM system will manage data management and enrichment and what functions it will perform. This document is crucial for all project participants, as it ensures a clear understanding of the technical solutions and functionalities that the system will offer.
The purpose of the technical and functional specification is:
- Comprehensive solution overview: The document provides a complete overview of the agreed solution, including all technical and functional components, allowing all stakeholders and project participants to understand what the project will involve.
- Clear goal communication: The specification clearly defines the main goal of the project and all other goals, which enables the coordinated work of all parties involved.
- A clearly defined development: The technical and functional specification serves as a guide for development teams that must implement the PIM system according to the requirements and specifications defined in the document.
By using the technical and functional specification as part of the project plan, we can ensure that the project will be carried out according to plans and expectations, thereby contributing to the success and efficiency of the entire project.
Solution
Based on received documents, company insights and the project vision, Pimcore was implemented to manage and enrich data. Pimcore now serves as the primary source for multilingual editing of descriptions, names, visual and video materials and storage of product technical data.
Employees at Olma can generate technical sheets for different languages and brands and catalogs for various measurement methods. Data from Pimcore is sent via GraphQL to external systems for product and industrial label creation. The system is scalable and it can be used for other sales purposes in the future, reducing manual work and data inconsistencies.
The biggest advantage of the Pimcore solution is that we can edit the data on one platform and this data is then updated on all other connected solutions.
Diagram of PIM system data management:

Description of the main functionalities
Data inheritance
With the introduction of Pimcore, we simplified the work process, especially when preparing and changing descriptions for products and versions of the “main” product. The system works according to the principle of “inheritance”. This means that by entering data on the “main” product, the entire content is transferred (inherited) to all products and brands listed under a certain “main” product.
Multilingual content editing
The challenge that Olma faced was the difficulty of maintaining content for different languages and different brands. Pimcore supports content editing for more than 13 different languages and more than 13 different brands, with easy expansion for additional languages and brands in the future.
Change traceability and version storage
In the past, OIma had a big challenge with tracking changes. They were often in a dilemma as to which version of the document was correct and currently valid. Pimcore provides change tracking, which means the user can see what changes were made, who made them and when and whether the change was published.
.png)
Data export
Generation of more accurate PDF files is now possible, which also enables formats with bleeds for printing.
Olma can get all the data from Pimcore and also generate a PDF document from it. We have also prepared an archive of past generated files for each product.
What the client said about working with us
“I am extremely happy with Optiweb’s PIM services. The team is able to quickly understand our needs and adequately cater to them. Here, the emphasis lies on the word adequately as you sometimes even surprise us with a solution that surpasses our expectations.
At the same time, I am happy that you’re the ones pushing us towards making progress, ensuring we finish the project as quickly as possible and then enjoy the fruits of our labor.
After the implementation of PIM, all our product data will be centralized in one place and all changes will be synchronized across the board (technical documentation, safety lists, stickers…).“
Aleš Hrobat
Business Development Manager @OLMA